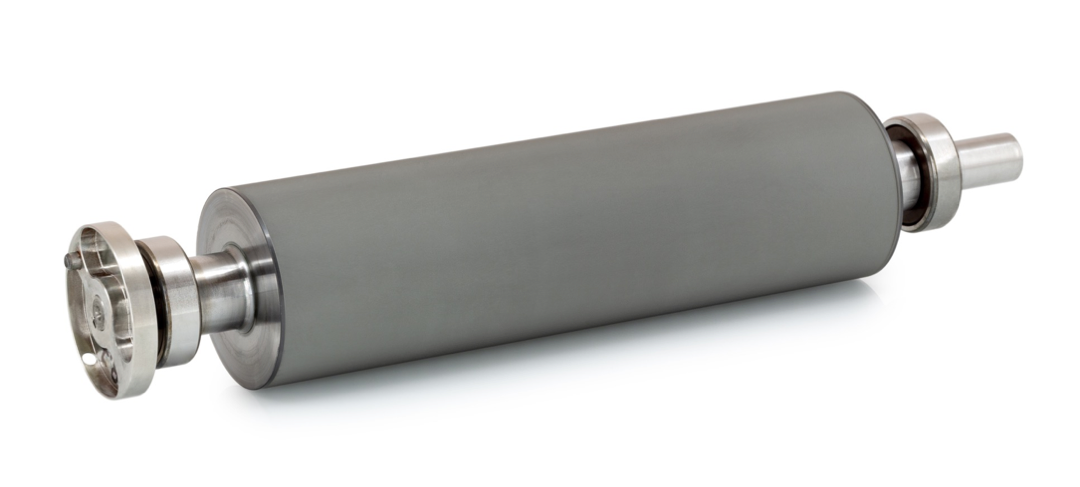
New graphene nanotube product particularly developed for EPDM rubber provides materials with anti-static properties and improves tear strength, overcoming the standard drawbacks of carbon black, polymer additives, multi wall carbon nanotubes, and other conductive agents on the market.
Electrically conductive rubbers are in high demand in many industries where rubber interacts with moving objects, which may cause a spark, or in explosive atmospheres regulated by electrostatic requirements. However, degradation of mechanical properties, elasticity, and color, along with compounding issues, are common drawbacks of typical conductive agents that arise from high working dosages. Graphene nanotubes, also known as single wall carbon nanotubes, stand out by showing results at extremely low working dosage starting from 0.15% for anti-static, static dissipative or conductive properties, while retaining or improving the mechanical properties of rubber.
A new solution based on TUBALL graphene nanotubes produced by OCSiAl makes it possible to achieve anti-static performance in mineral filler-based EPDM formulations, as well as improvements in tear strength and tensile performance by up to 70% without degradation of elastic properties or hardening. “About 10% of conductive polymer is normally used to reach the same resistivity level, leading to a significant negative impact on mechanical properties and unstable anti-static performance due to release of this additive to the material’s surface. On the other hand, use of carbon black results in dusty production, hardening, and carbon release to the surface of molded parts, which leads to black marks,” explains Ekaterina Gorbunova, OCSiAl Vice-President for Elastomers. “For TUBALL MATRIX preparation, we use a triple system, with graphene nanotubes being dispersed in the plasticizer and the polymer, where the plasticizer facilitates proper dispersion and retains elastic behavior, and the crosslinkable polymer interacts with the material medium for better mechanical performance and creation of a 3D conductive network built by nanotubes. In other words, this solution makes it possible to produce low-hardness compounds with the required conductive performance, which was not possible using conventional additives.”
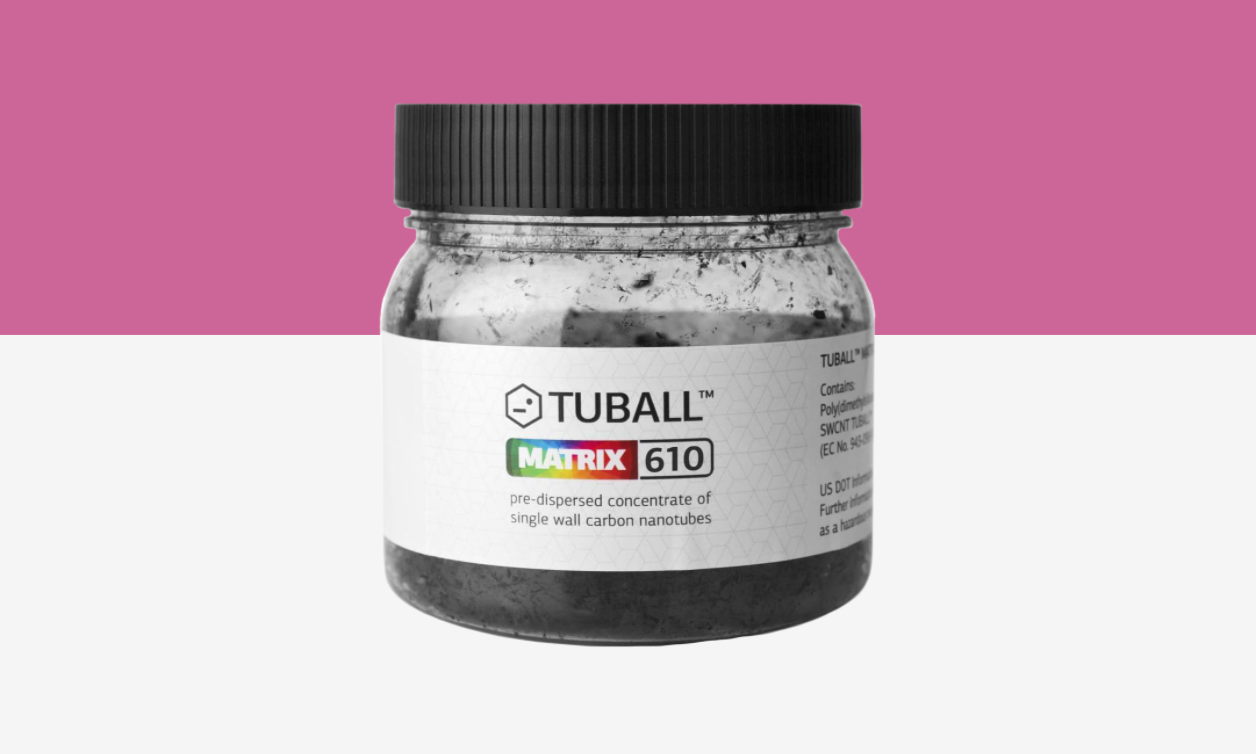
Some of the main sectors to use anti-static EPDM are the conveyor manufacturing, industrial roller, cable accessory, and automotive industries, in a wide range of products where stable electrically conductive properties are required in combination with a long service life and color options.
The launch of a new product series for EPDM rubber is only the first step in industrializing and expanding graphene nanotube solutions for various types of rubbers. OCSiAl has developed and is preparing to scale up production of products for electrically conductive and mechanically strong FKM, natural rubber, BR, NBR, SBR and silicones, and received wide adoption in electronics, automotive, oil & gas, and other industries related to static sensitive or harsh environments.
Learn more about graphene nanotubes for electrically conductive rubbers at tuball.com.