- Graphene nanotubes facilitate the use of composite pipes at high-risk facilities, boosting safety by reducing spark risk.
- The working loading of nanotubes is hundreds of times lower than that of carbon black, and they grant permanent anti-static properties in contrast to liquid agents.
- The technology works with most resin types and manufacturing processes.
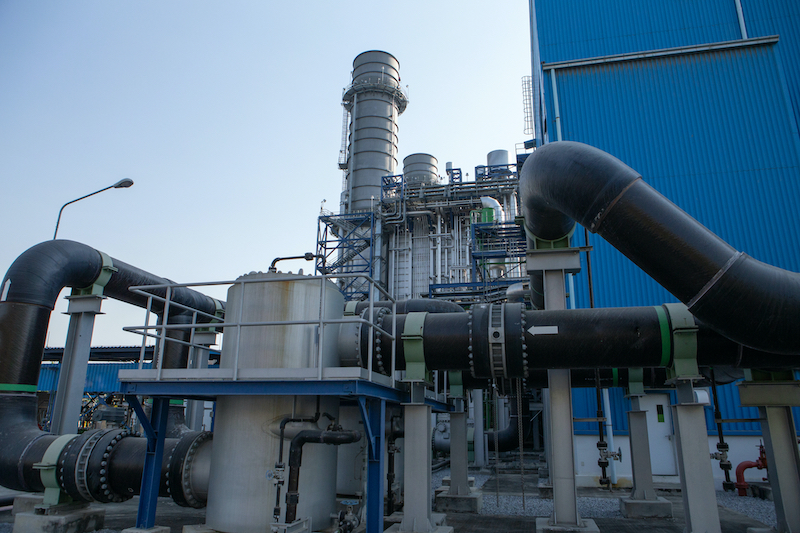
The growing use of composite pipes is a result of their ability to counter inherent drawbacks of steel pipes, such as corrosion, fatigue, dependency on temperature, heavy weight, rigidity, and high CO2 footprint during production and installation. But for some specific applications, a key issue in replacing steel lies in the originally dielectric properties of a composite pipe. Explosion is a common hazard at extraction and processing plants, and chemical and production facilities, where highly flammable liquids are transported and poured, or powdered combustible materials are handled. To eliminate the risk of explosion, composite pipes should dissipate static charges generated by motion and rubbing one material against another. As an example, according to ISO 14692 Petroleum and natural gas industries – glass-reinforced plastics piping, the required level of volume resistance should be lower than 10^4 Ohm*m, which is equal to lower than 10^6 Ohm*cm.
Graphene nanotubes dispersed in resin grant permanent and uniform anti-static properties to pipes and ensure safety from sparks, a frequent cause of ignition and explosion. The attraction of this solution lies in the simplicity of granting anti-static properties to composite material and its uniformity. Previously, the usual method was to coat the fiber-glass surface with an anti-static coating, to apply a carbon veil as a separate layer, or to add carbon black inside the resin. “The coating, unfortunately, is subject to abrasion loading and other durability issues and there is a potential need for further recoating. Carbon veils or rovings can require more labor and production time, and can also be challenging to produce rotating parts with the required quality. Also, carbon black leads to degradation of mechanical properties and unwanted dust formation,” said Hendrik Janssen, Technical Support Engineer for EMEA, OCSiAl Group.
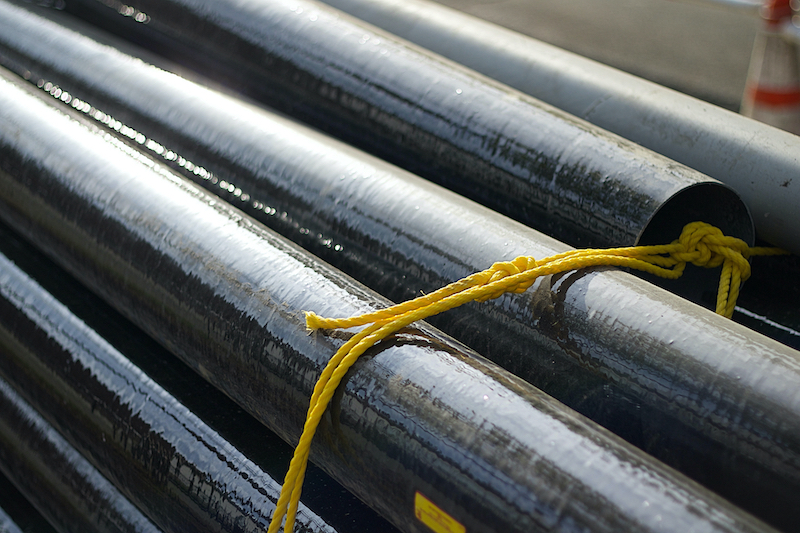
The practical solution, welcomed by pipe manufacturers, is to replace 4–15% of carbon black with 0.02–0.05% of graphene nanotubes to achieve a permanent and stable level of resistivity of 10^4–10^6 Ohm*cm in GFRP pipes. Nanotubes create a homogeneous and stable conductive network inside epoxy, polyester, and vinyl-ester that ensures that every part of a pipe can dissipate dangerous static charge and do this throughout the whole service life of the pipe. Nanotube concentrates by OCSiAl based on various polymer carriers are easily compatible with key manufacturing technologies, such as SMC, BMC, spray-up, filament winding, pultrusion, and hand layup.
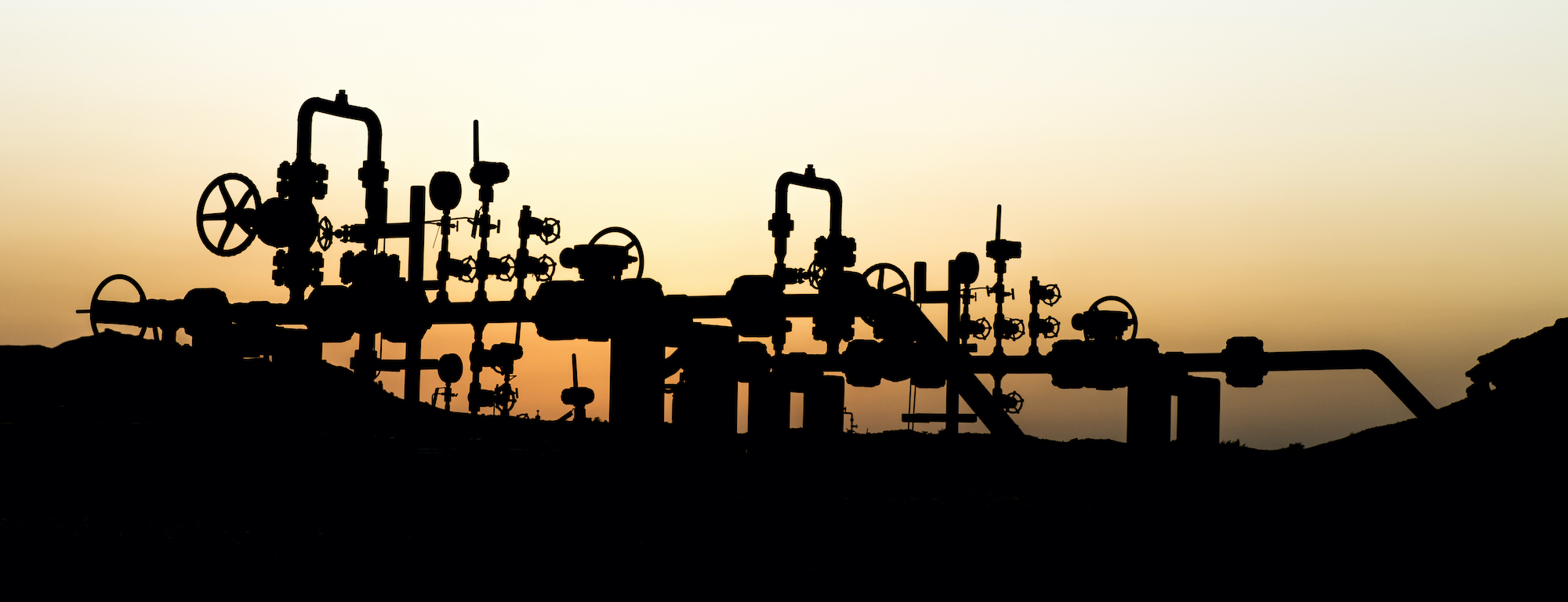
“The value proposition nanotubes bring is two-fold. On the one hand, nanotubes facilitate a wider use of composite pipes, which eliminate the corrosion problem, slash the cost of infrastructure, and offer CO2 savings compared to the installation and maintenance of steel pipes. On the other hand, nanotubes significantly improve the safety of the high-risk facilities, which is crucial for the oil & gas industry, chemical plants, and mines,” added Mr. Janssen.
More info on nanotubes in composites at tuball.com.