- Polyurethane rollers with added conductivity save money by minimizing damage to electronic products when materials become electrically charged by the triboelectric effect during functioning of the roller in its application.
- A new product launched by I.B. Moore, a US-based company, incorporates the innovative graphene nanotubes that make the complete manufacturing process efficient, production worthy, and sustainable.
- Current applications for this new product include the printing, packaging, and converting industries; voting, lottery, and paper folding machines; money handling equipment; autonomous mobile robots (AMR); automated picking and sorting machines; and automated guided vehicles (AGV).
Until recently, the common technologies on the US market to grant anti-static properties to PU rollers were carbon black and organic ionic-conductive agents, which lead to a set of limitations. The high level of carbon black required to meet anti-static requirements results in a much thicker mixture and thus difficulties in processing the batch. Ionic-conductive agents lead to only mild anti-static volume resistivity readings rather than higher conductive values. Also, the physical properties of the final product, such as compression set and hardness, can be hindered.
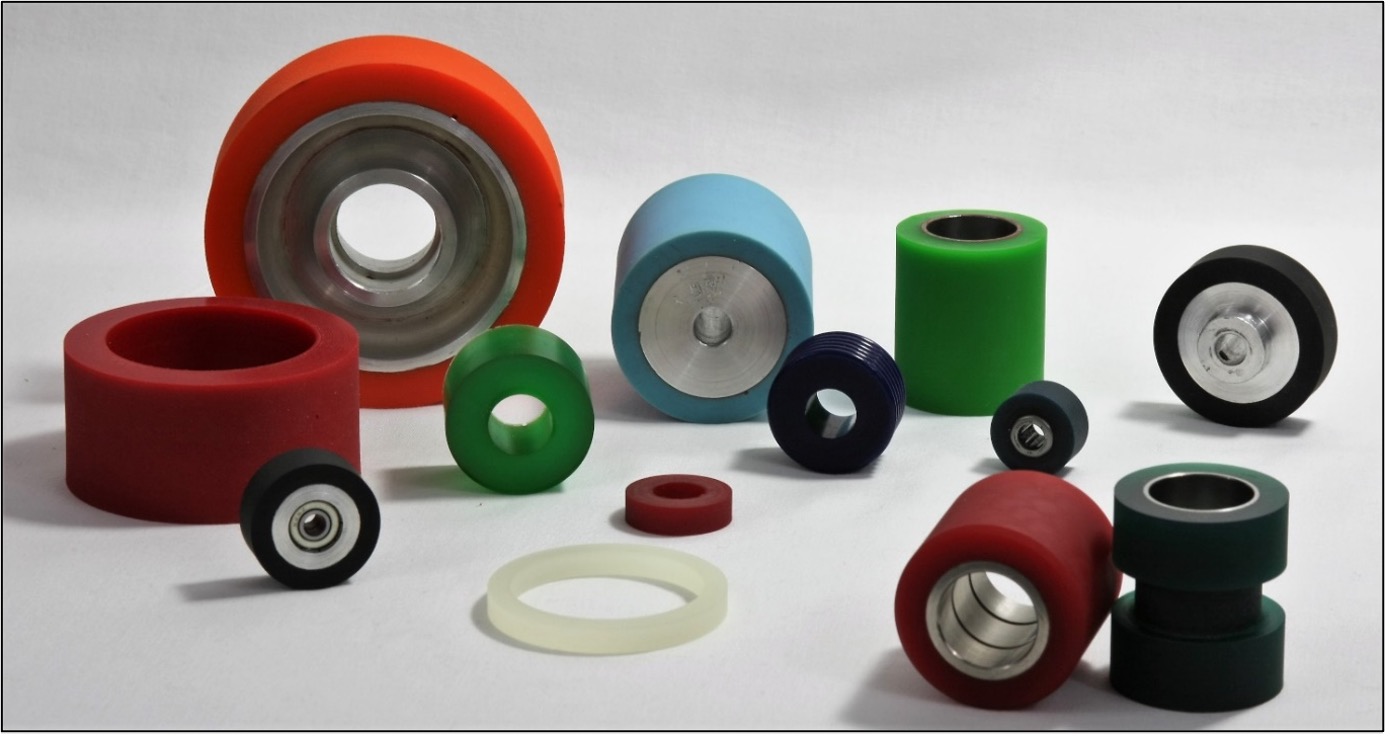
I.B. Moore pushes the limits of its urethane rollers, making it possible to introduce graphene nanotubes into non-conductive products to increase their overall performance and efficiency. The basis for this is a new set of properties enabled by graphene nanotubes: a more stable and wider range of resistance levels compared to ammonium salts, all grades of urethane hardness (45A to 96A - Shore A) and leaving a non-marking surface (no black “smearing” traces) on the surface of output products (fabric, paper, film, etc.) thus preventing the occurrence of malfunction and/or rejects.
“To obtain volume resistivity within the range of 109–104 Ω·cm, it is sufficient to add OCSiAl’s graphene nanotubes in a working concentration that is 100 times less than that of ammonium salts and 500 times less than that of carbon black. Such low loadings and nanotubes’ intrinsic morphology do not diminish the useful physical properties of the final product. The addition of nanotubes does not interfere with our established manufacturing processing procedures, which allows for an efficient and production worthy process,” said Danny R. Siders, Managing Member, I.B. Moore Company, LLC.
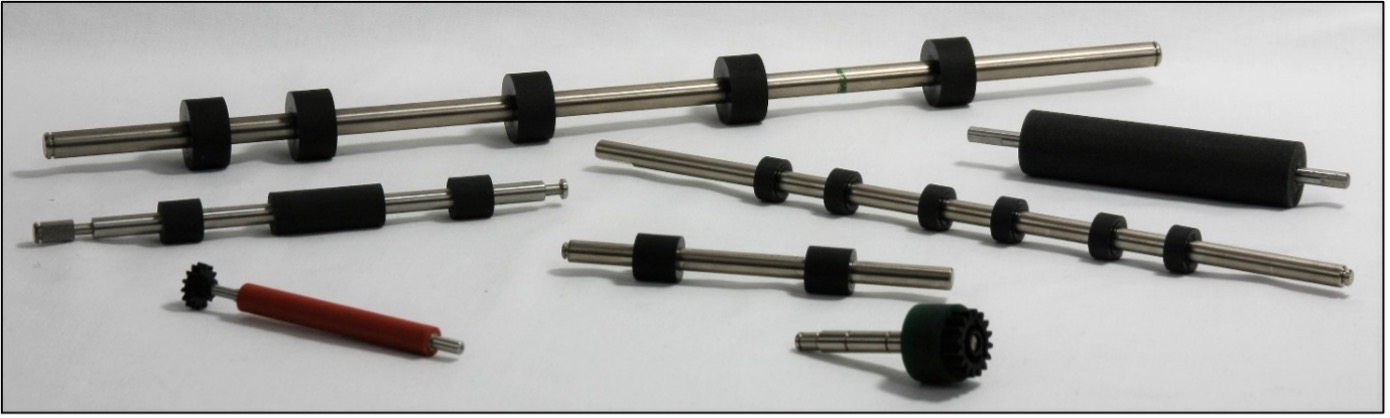
Such anti-static rollers are engineered to serve a neutralizing function in a variety of industries, saving money as they can prevent damage to sensitive electronic devices during handling, assembly, and transportation. “This new graphene nanotube technology gives the opportunity to formulate materials for other critical static-dissipation applications and meet electrical project needs,” added Danny R. Siders.
Headquartered in Luxembourg, OCSiAl is the world’s leading manufacturer of graphene nanotubes, also known as single wall carbon nanotubes. It employs about five hundred people worldwide in locations including the United States, Europe, and Asia.
Website: tuball.com
I.B. Moore Company, LLC has manufactured custom rubber and urethane rollers for over five decades at its 30,000-square-foot facility located in Lexington, Kentucky, USA. I.B. Moore custom formulates liquid castable polyurethanes to meet unique customer requirements for various stringent material and dimensionally tight-tolerance applications.
Website: ibmoore.com