- A novel conductive PSA exhibits remarkable transparency and maintains stable electrical conductivity throughout its lifespan.
- Graphene nanotubes inside adhesives make it possible to reduce the number of layers, improving cost-efficiency of processing.
- The new set of properties enabled by nanotubes expands PSA’s standard range of applications, encompassing optical films, flexible displays, and more.
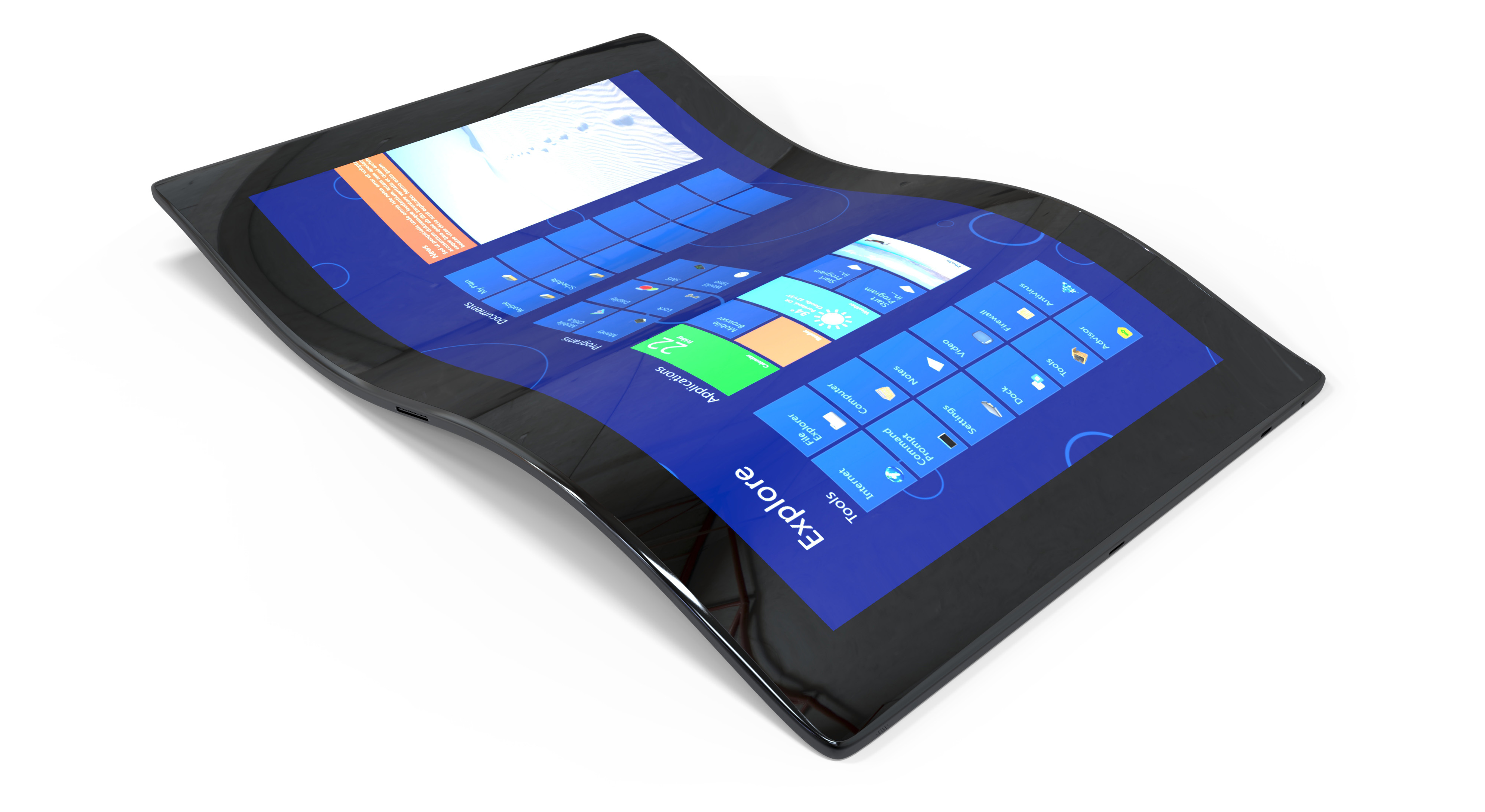
The global market for conductive pressure-sensitive adhesives (PSAs) is forecast to reach $12.5 billion by 2025, driven by wide-ranging applications. To keep growing, the industry has always been on the lookout for solutions for anti-static PSA, without drawbacks such as degradation of conductivity over time, low transparency, or limited flexibility.
OCSiAl’s exceptional graphene nanotube-based solution addresses these issues, ushering in a new era of silicone PSA technology. The user-friendly nanotube dispersion TUBALLTM MATRIX 617 results in excellent electrical conductivity combined with more than 90% transparency in a wide range of peeling-strength PSA films.
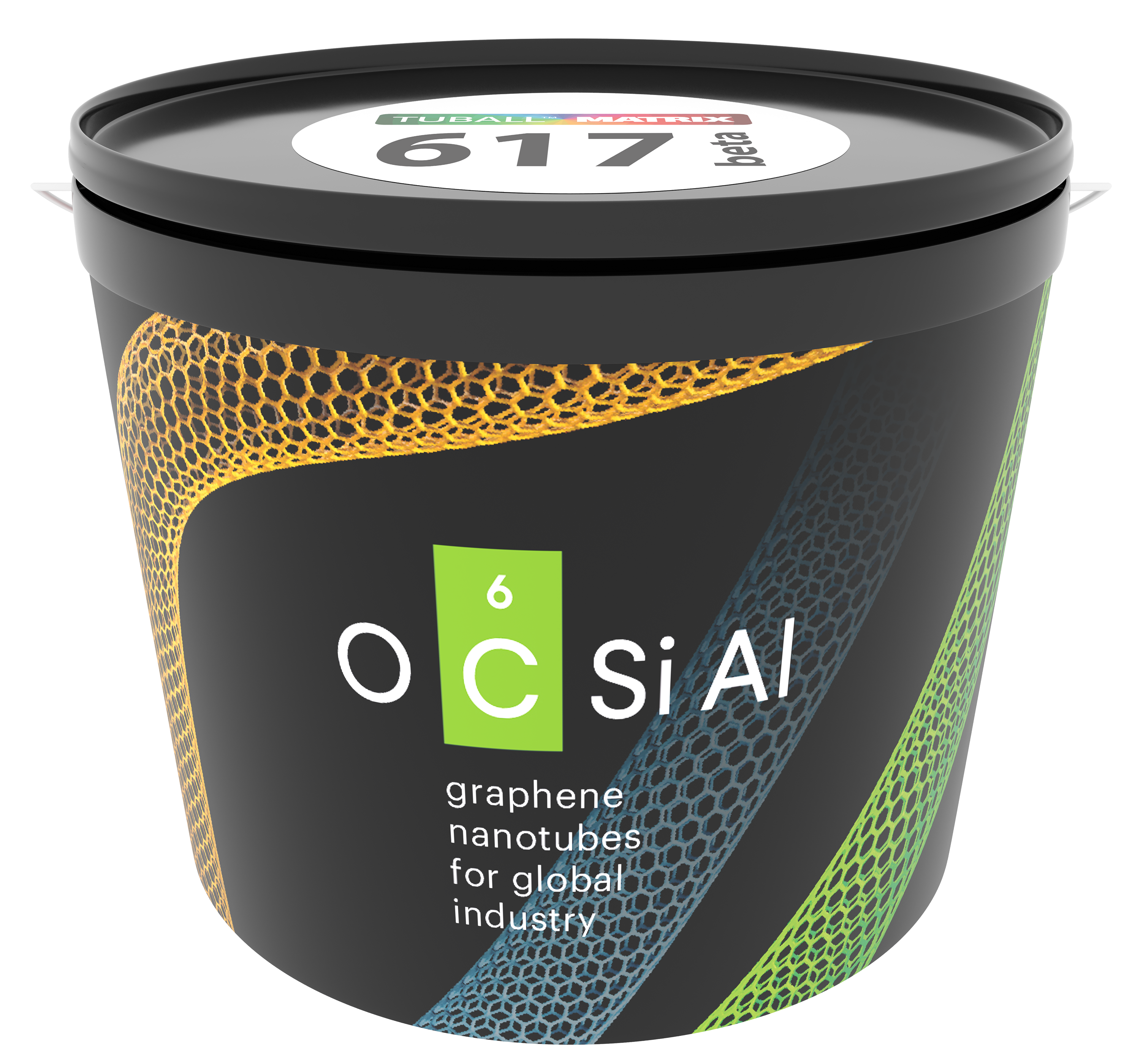
The nanotube concentrate can be seamlessly integrated into silicone PSA resins without altering standard mixing processes or equipment. “The recently developed product is a concentrate based on a user-friendly reactive silicone polymer and pre-dispersed TUBALL™ graphene nanotubes specifically designed for silicone PSA systems. It offers an extremely fine quality of nanotube dispersion and is easier to handle in specific applications, notably in a low solid-content systems,” said Ekaterina Gorbunova, Development and Support Leader for Elastomers and Vice President at OCSiAl Group.
Just 0.2% TUBALL™ MATRIX 617 ensures uniform dispersion of conductive particles inside PSA film. This results in a stable surface resistivity of less than 107 Ohm/sq, even after multiple peelings and exposure to high temperatures, which makes it possible to meet strict requirements for stable touch screen operations. In comparison, traditional PSA on conventional polymer primer can only achieve surface resistivity of 1010 Ohm/sq, because above this level, it tends to become unstable over time.
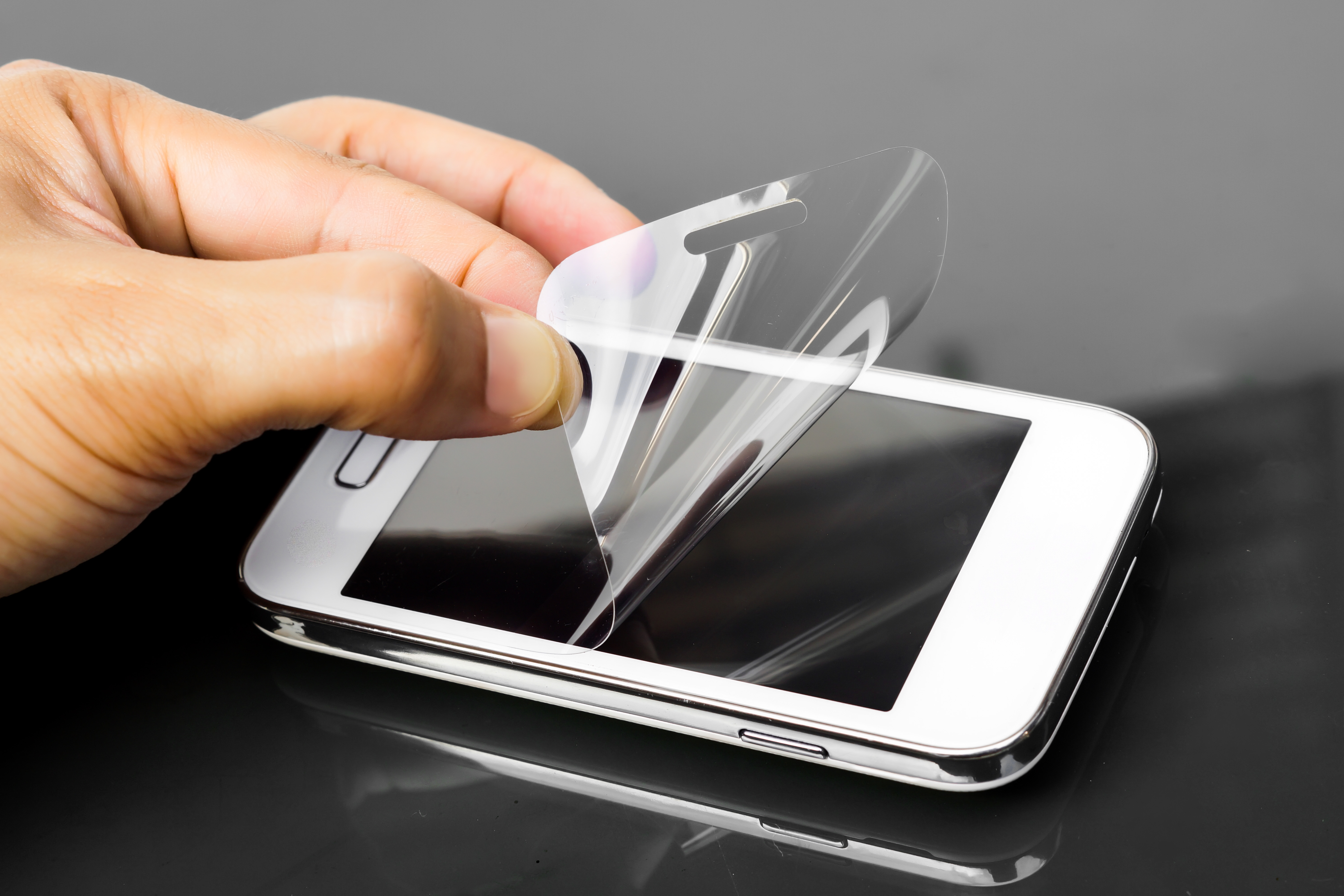
The newly developed, permanently conductive silicone PSA formulations reduce the number of layers needed, eliminate the requirement for a primer, and improve cost-efficiency. The outcome is a new generation of fine, flexible, transparent, sensitive films suitable for applications in high demand in electronics, medical devices, the automotive industry, and packaging.
To learn more, watch our processing guide on anti-static PSA: https://youtu.be/tACryiEbGF8
To request a sample visit tuball.com