- Ultralight, durable composite sleeves with graphene nanotubes avoid build-up of static electricity and can therefore be used with solvent ink, in addition to water and UV inks.
- 0.02% graphene nanotubes results in <106 Ω·cm volume resistance, which enables improved printing quality by dissipating the static charge accumulated due to friction.
- An additional advantage is the flexibility in adjusting a cylinder’s color palette.
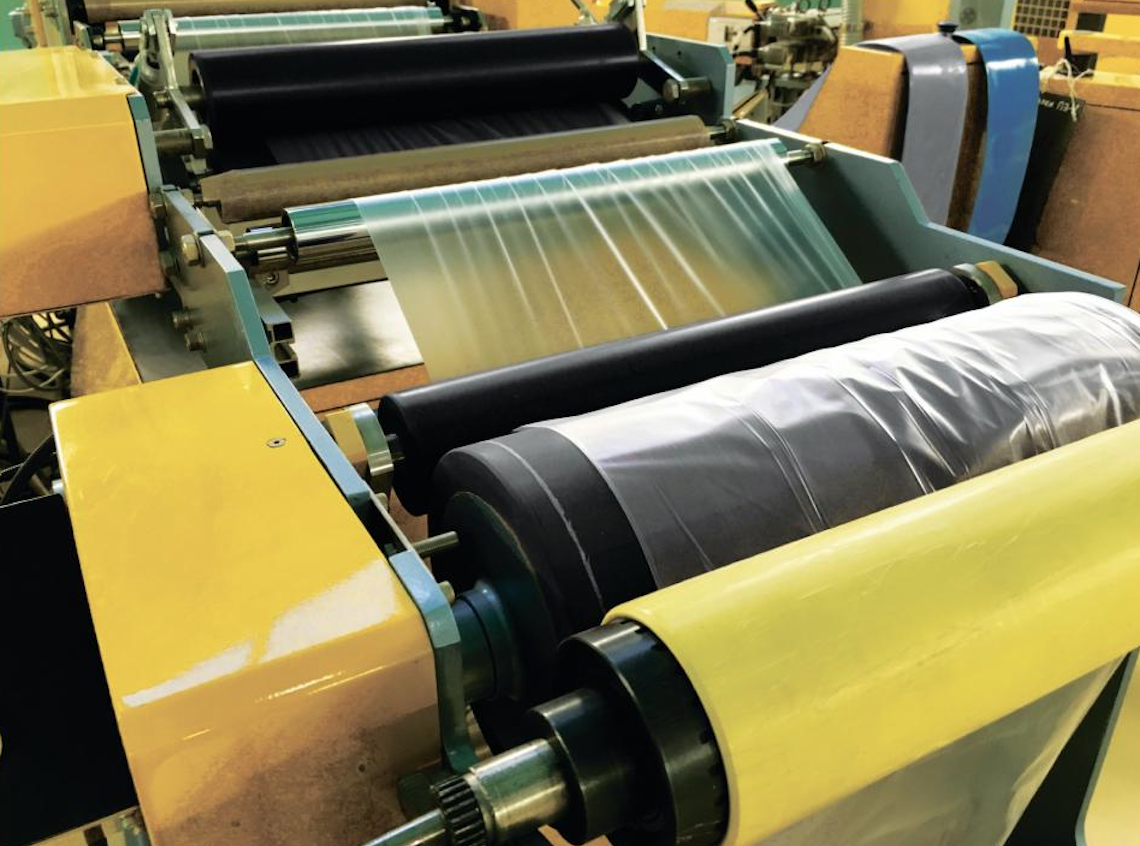
The cylinder is one of the key components in rotary printing that have the greatest impact on printing quality and production cost. Its high rotation speed during printing produces static electricity that leads to paper sticking, worsening of printing quality, and—in rare cases when solvent-based ink is used without conducting sleeves—even to explosions, slowing down the printing process and increasing operational costs. This could even be dangerous for the operators of the machines, so it is the matter of safety. To avoid this, composite cylinders should be modified with electrically conductive additives so as to dissipate accumulated static electricity. One of the most widespread additives for composite sleeves is carbon black. But its main disadvantage lies in the high working dosage required to achieve targeted conductivity. This causes an increase in viscosity, a negative impact on the mechanical performance of the base material, dust, and various other issues during the working process.
A European tooling producer has expanded its production line with an ultralight composite printing cylinder by introducing to its epoxy compound a TUBALL™ MATRIX pre-dispersed concentrate of graphene nanotubes, produced by OCSiAl. Graphene nanotubes add value in the new product by providing superior electrical conductivity to the base material, while retaining and even enhancing mechanical properties, and otherwise minimally affecting the host matrix.
%20copy.jpg)
“The obtained electrical conductivity of <106 Ω·cm independent of humidity improves the performance of the new sleeves by dissipating accumulated static electricity. Weight reduction was achieved due to the overall optimization of the technological process, the coating method, and replacing 20 wt.% of carbon black with approximately 0.01–0.05 wt.% of graphene nanotubes,” said Andrew Dubrovskiy, Technical Sales Manager for Coating & Thermoplastics for EMEA, OCSiAl Group. The new technology for sleeve production allows a higher working speed of rotation and flexibility in adjusting product dimensions, such as length, thickness, and outer diameter.
Another European producer achieved the target static conductivity by reaching a volume resistance of <107 Ω·cm using 0.015 wt.% of graphene nanotubes. No changes of the mechanical properties and very high efficiency were observed in the resulting material, in contrast to carbon black and most other additives. This makes it possible to maintain high hardness and no deformation. Moreover, the easy-to-handle nanotube concentrate form doesn’t require changes in the standard production process. The tiny quantity of nanotubes avoids carbon black’s negative graying effect on the color, making it possible to expand the range of colors of conductive sleeves. Finally, using sustainable graphene nanotubes makes it possible to make production clean and cost-efficient.
Learn more on graphene nanotubes at tuball.com.