- OCSiAl has launched a new graphene nanotube concentrate for PA, filled PPS, ABS, TPU, and PC.
- The new product provides targeted conductivity in thermoplastics produced by injection molding at working loadings starting from 0.1 wt.% of nanotubes in the final system.
- This approach allows makers to optimize the painting process and reduce the final production cost.
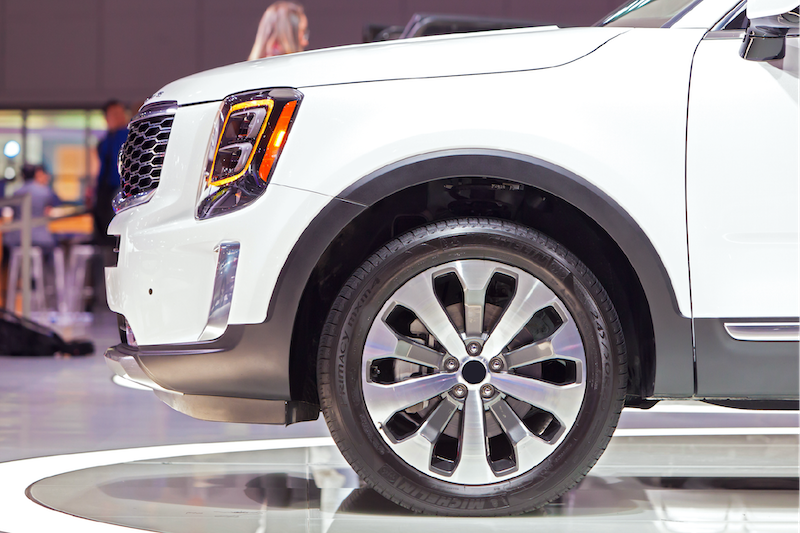
Painting of exterior automotive parts, such as fenders, bumpers, tanks flaps, grilles, mirror housing, exterior trims, and rear quarter panels, is complicated by the necessity of separate operation lines for metallic and polymer components, as plastics are insulative, which makes in-line electrostatic spray painting impossible. This leads to additional expenses and slows down the whole painting process. To overcome this, manufacturers of automotive parts should wisely choose temperature-stable thermoplastic grades and modify these systems with electrically conductive additives. The most widespread is carbon black. However, because of their high working dosage required, car end parts with additives demonstrate worsened mechanical properties and processing challenges.
OCSiAl, the world’s largest manufacturer of single-wall carbon nanotubes, also known as graphene nanotubes, has launched the new easy-to-use TUBALL™ MATRIX 822 graphene nanotube concentrate specifically designed for PA, filled PPS, ABS, TPU, and PC compounds for injection molding. Introducing these nanotubes creates a permanent and homogeneous electrical conductivity without “hot spots” in the range of 10^5–10^9 Ω·cm, while retaining the original key mechanical properties, such as durability and strength, and minimally impacting the host polymer matrix. Furthermore, a low working dosage of 0.1-0.3 wt.% of graphene nanotubes demonstrates only a limited effect on rheological properties and processability.
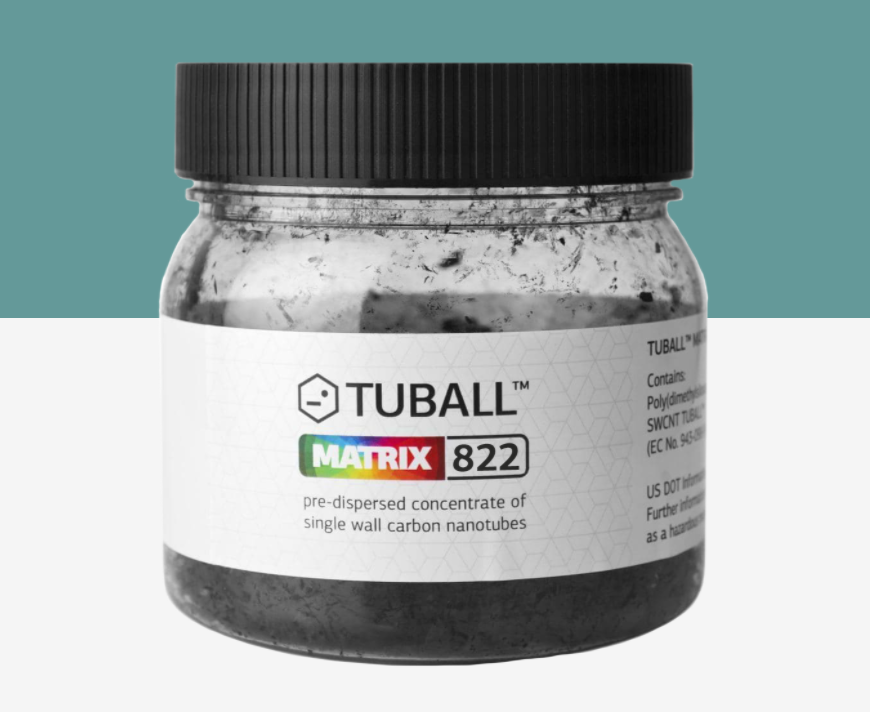
Graphene nanotube concentrate now enables in-line e-painting of plastic exterior parts together with metal components using electrophoresis, where previously, separate production lines were required. Manufacturers of polymer injection molded parts for automotive, industrial, construction, mining, and other applications now have opportunity to reduce production costs and the number of rejected final parts without changing standard operating processes by using high-performance graphene nanotubes.
“The new product will also be valuable for improving automotive safety and tracking systems: graphene nanotubes allow makers to produce high-quality electrically conductive thermoplastic products without compromises in terms of overall product mechanical performance or durability,” said Vladimir Kravchenko, Development and Support Leader for Thermosets, OCSiAl Group. “We already see demand from manufacturers of fuel system parts including quick connectors, fuel pumps, valves, filter housings, EV-battery caps, and other car components.”
Request a sample at tuball.com