- Daikin and OCSiAl have developed graphene nanotube solutions for highly durable, electrically conductive FKM compounds with improved heat stability.
- In-conditions tests showed almost double the tear strength and better elastic properties even at elevated temperatures of 200°C.
- An increase in the mechanical properties of FKM is highly desirable in the automotive, oil & gas, aerospace, and other industries with extreme operating conditions.
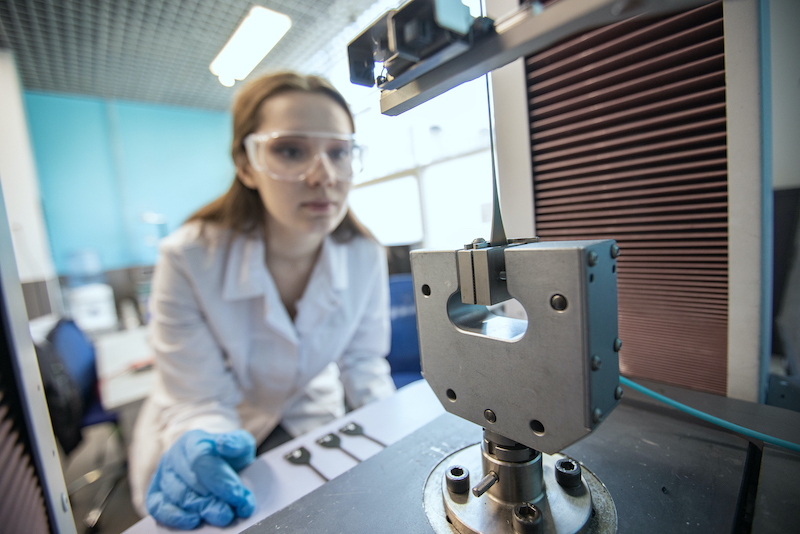
To meet market demand, leading graphene nanotube manufacturer OCSiAl and a pioneer in fluorine technologies, Daikin Industries, have jointly developed a graphene nanotube technology for highly durable, electrically conductive FKM compounds with improved heat stability.
Outstanding chemical and high-temperature resistance make fluoroelastomers (FKM) a material of choice for sealing elements exposed to harsh environments. The automotive, oil and gas, aerospace, and other industries where conventional elastomers hardly withstand severe operating conditions, are boosting the growth of the FKM market. Specific applications demand further improvement in FKM mechanical performance, such as improved modulus, tear resistance, and tensile strength. Improved electrically conductive properties are required in electric vehicles and various ESD control areas.
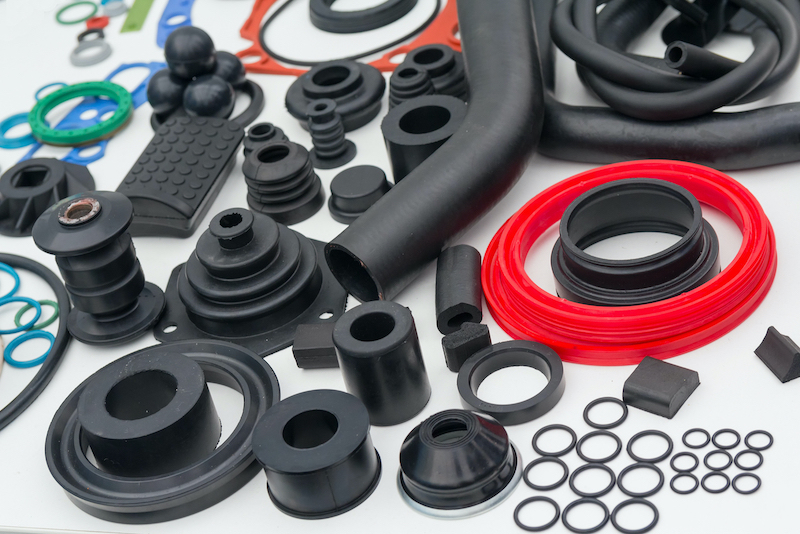
“Standard conductive fillers bring a number of negative trade-offs to elastomers in terms of flexibility and elasticity. This leads to hardening and a reduced life cycle of the final parts, which is critical in FKMs where the original hardness is already high,” explains Junpei Terada, Marketing Department, Chemicals Division, at Daikin Industries, Ltd.
Introducing just 0.3% of TUBALL graphene nanotubes produced by OCSiAl to FKM rubber makes it possible to obtain anti-static FKM compounds with volume electrical resistivity below 10 Ω∙cm. Such a low working dosage allows producers to avoid the negative trade-offs typical for other conductive additives in terms of hardness, extrusion rate, and degradation of mechanical strength and elastic behavior.
To guarantee material stability and durability, the rubber’s properties under service conditions, particularly at high temperature, are studied. Tests at 200°C show that FKM samples modified with nanotubes demonstrate improvement in tear strength of up to 61%, tensile strength of up to 92%, M50 of up to 71%, and better elastic properties, while also retaining hardness. Besides this, assessment after heat aging also shows significantly improved mechanical property stability and retained elasticity compared to reference material: tear strength almost 80% higher, modulus up to 54% higher, and retained elastic properties were indicated after aging at 230°C.
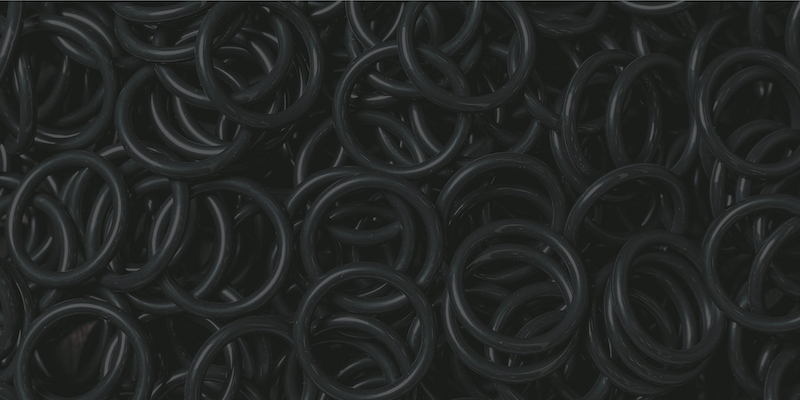
Currently, applications of innovative nanotube-reinforced fluoroelastomers are being developed by a number of companies in the automotive and equipment construction sectors, reaching higher performance for seals, O-rings, hoses for hybrid vehicles, rubber jacketing materials, heat-resistant cords and plates, as well as rubber parts used in robotic factories.
Learn more on graphene nanotubes at tuball.com.